Stray-field robust ASIL C ready Hall-effect position sensor family for high-speed e-motor applications
The HAL 302x family from Micronas is designed to meet the demand for robust motor position sensing in environments with stray magnetic fields, while also aligning with ISO 26262 compliance in automotive and industrial developments. Consisting initially of two models, HAL 3020 and HAL 3021, these sensors offer differential and single-ended sine and cosine analog outputs for standard angle calculation through an external microcontroller/ECU. HAL 3020 is well-suited for cost-effective applications such as electric pumps or valves, easily integrating with TDK’s Micronas embedded motor controller portfolio for enhanced motor control precision and safety. On the other hand, HAL 3021 is ideal for high-speed sensing applications like electric power steering, e-motors (e-axle), electric brake boosters, and electromechanical braking (EMB).
HAL 3020 and HAL 3021
Fast Stray-Field Robust Motor Position Sensor
HAL 302x is a fast 2D angular position sensor family addressing the need for stray-field robust motor position sensing as well as the ISO 26262 compliant development. This new sensor family features differential or single-ended sine and cosine analog outputs with integrated wire-break detection. The rotation angle of a magnet can be calculated by an external A/D-converter and a microcontroller/ECU.
This new family has two members, HAL 3020 and HAL 3021. Both members measure, based on Hall-effect technology, vertical magnetic-field components (BZ). Speciality of HAL 3021 is that the device offers a higher robustness against static and dynamic mechanical tolerances.
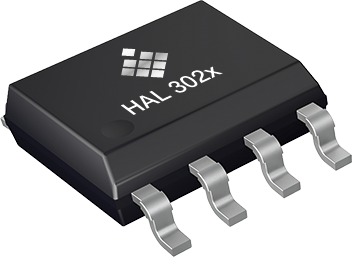
HAL 302x Sensors: 360° Precision with Magnetic Resilience for Next-Gen Electric Motors
HAL 302x sensors can measure a full 360° rotational angle by evaluating vertical magnetic-field components (BZ). Both sensors are able to suppress external DC and AC magnetic stray fields (ISO 11452-8). By suppressing harmonic disturbances in the stimulation signals through device-internal calculations, a simple and cost-efficient two-pole ferrite magnet in an on-axis (end-of-shaft) configuration is sufficient to measure the absolute angular position. Thanks to the inherent stray-field robustness, the need for expensive magnetic shielding and the use of stronger target magnets is eliminated. This gives more flexibility in the design and production of next-generation electric motors to be used in hybrid and electric vehicles.
A key strength of HAL 3021 is that the device offers best-in-class robustness against static and dynamic mechanical misalignments, such as off-axis displacement, airgap variation and tilt. This ensures highly reliable and efficient field-oriented control of motors over their lifetime. To lower the load of the ECU, the sensor can compensate on-chip for the main sensor- and system-level non-idealities, like sine and cosine amplitude mismatch, offset errors, (absolute) 0-angle, and orthogonality errors.
HAL 302x is defined as Safety Element out of Context (SEooC) ASIL C ready according to ISO 26262, supporting system level integration up to ASIL D. The sensor integrates various safety monitoring functions, which help to increase diagnostic coverage and simplify the external safety supervision on the ECU side.
Get in Contact with our Experts